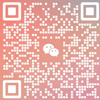
The electronics industry is large and growing rapidly in every aspect of modern life, including smartphones, personal computers and electric vehicles. Laser technology plays a vital role in all of this, driving the efficiency and refinement of the electronic component production process. laser marking technology plays a key role in the marking of electronic components, especially when the smallest and most sensitive components need to be permanently marked, laser is undoubtedly the best choice.
Advantages of laser markers
Marking lasers are the tool of choice for marking sensitive electronic components. Their precise energy input and stable laser characteristics ensure process reliability and are suitable for a wide range of component materials. The flexibility of these lasers allows them to adapt to different production requirements, whether metal, plastic or other composite materials. The durability of laser marking is also an important feature, and it can maintain clear and long-lasting marks in harsh environments.
laser marking of printed circuit boards (PCBs)
Printed circuit boards are the core component of every electronic product, and their traceability is crucial. By marking PCBs with text, serial numbers, barcodes or data matrix codes, production errors can be quickly identified and entire batches can be traced. Due to the limited space and sensitive materials of PCBs, TRUMPF laser marking machines ensure efficient and reliable laser marking with their high peak pulse power and excellent focusing capabilities, meeting the industry's dual needs for precision and speed.
Semiconductor laser marking
As semiconductor technology advances, component sizes are shrinking, and the requirements for marking processes are increasing. Marking semiconductor components not only requires clear and machine-readable fonts, but also protects surrounding materials during the marking process. Pulsed lasers are ideal for this task, with fast, precise characteristics that can easily mark micro-components while effectively protecting surrounding sensitive areas from damage.
Laser marking of flame-retardant plastics
Many electronic components, such as switches and connectors, are made of flame-retardant plastics. The key to achieving high-quality laser marking is to use the right wavelength to induce thermal changes in the plastic. When using a UV marking laser (with a wavelength of UV light) for marking, flame-retardant plastics can absorb laser energy more effectively, and the marking process is achieved through a photochemical reaction on the surface of the component, ultimately achieving a high-quality marking effect. This method not only improves the clarity of the mark, but also enhances the durability of the mark, allowing it to remain stable in a variety of working environments.
Summary
Laser marking technology is driving the continued development of the electronics industry with its high efficiency, precision and flexibility in the application of electronic components. With the continuous advancement of technology and changes in market demand, laser marking will continue to provide better solutions for the production of electronic products and contribute to the innovation and sustainable development of the industry.
Please leave the message you want to inquiry. We will reply you as soon as possible within 24 hours.
Please leave the message you want to inquiry. We will reply you as soon as possible within 24 hours.