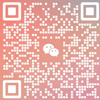
In the industrial field, laser welding machines have become an emerging key technology in industrial laser welding processing due to their significant advantages such as fast welding speed, high precision, high efficiency and smooth and beautiful welds. At present, laser welding machines are widely used. However, in practical applications, it is necessary to reasonably select laser welding machines and set appropriate welding process parameters according to the characteristics of the materials to give full play to their advantages and ensure welding quality and efficiency.
Laser welding machines have good welding effects on carbon steel, but the quality is affected by impurities. Carbon content exceeds 0.25% and needs to be preheated. When welding steels with different carbon contents, the welding gun should be biased towards the low-carbon side. When the carbon content is high, the sensitivity of welding cracks increases. Medium and high carbon steels and ordinary alloy steels can be welded with laser welding machines, but preheating and post-weld treatment are required to prevent cracks.
For laser welding of low-alloy high-strength steel, as long as the appropriate welding parameters are accurately selected, the laser welding machine can make the welded joint obtain mechanical properties equivalent to those of the parent material.
Generally speaking, it is easier to obtain high-quality joints by using a laser welding machine to weld stainless steel than by conventional welding. Laser welding, with its fast welding speed and small heat-affected zone, effectively alleviates the adverse effects of overheating and large linear expansion coefficient during stainless steel welding, and its welds will not have defects such as pores and inclusions. Compared with carbon steel, stainless steel has lower thermal conductivity, higher energy absorption rate, and higher melting efficiency. Laser welding machines can achieve deep melting and narrow welds.
Laser welding machines are prone to incomplete fusion and incomplete penetration when welding copper and copper alloys, so energy-concentrated, high-power laser welding machines should be used, and preheating measures should be taken. When the workpiece is thin or the structural rigidity is small, and there is a lack of measures to prevent deformation, it is easy to produce large deformation after welding with a laser welding machine; when the welding joint is subject to a large rigidity constraint, welding stress is easy to generate. In addition, thermal cracks and pores are also common defects in laser welding of copper and copper alloys.
Aluminum and aluminum alloys are highly reflective materials. When using a laser welding machine for welding, as the temperature rises, the solubility of hydrogen in aluminum increases sharply. Dissolved hydrogen will become a defect source in the weld, resulting in more pores in the weld. During deep penetration welding, cavities may appear at the root, and the weld bead is poorly formed.
Please leave the message you want to inquiry. We will reply you as soon as possible within 24 hours.
Please leave the message you want to inquiry. We will reply you as soon as possible within 24 hours.